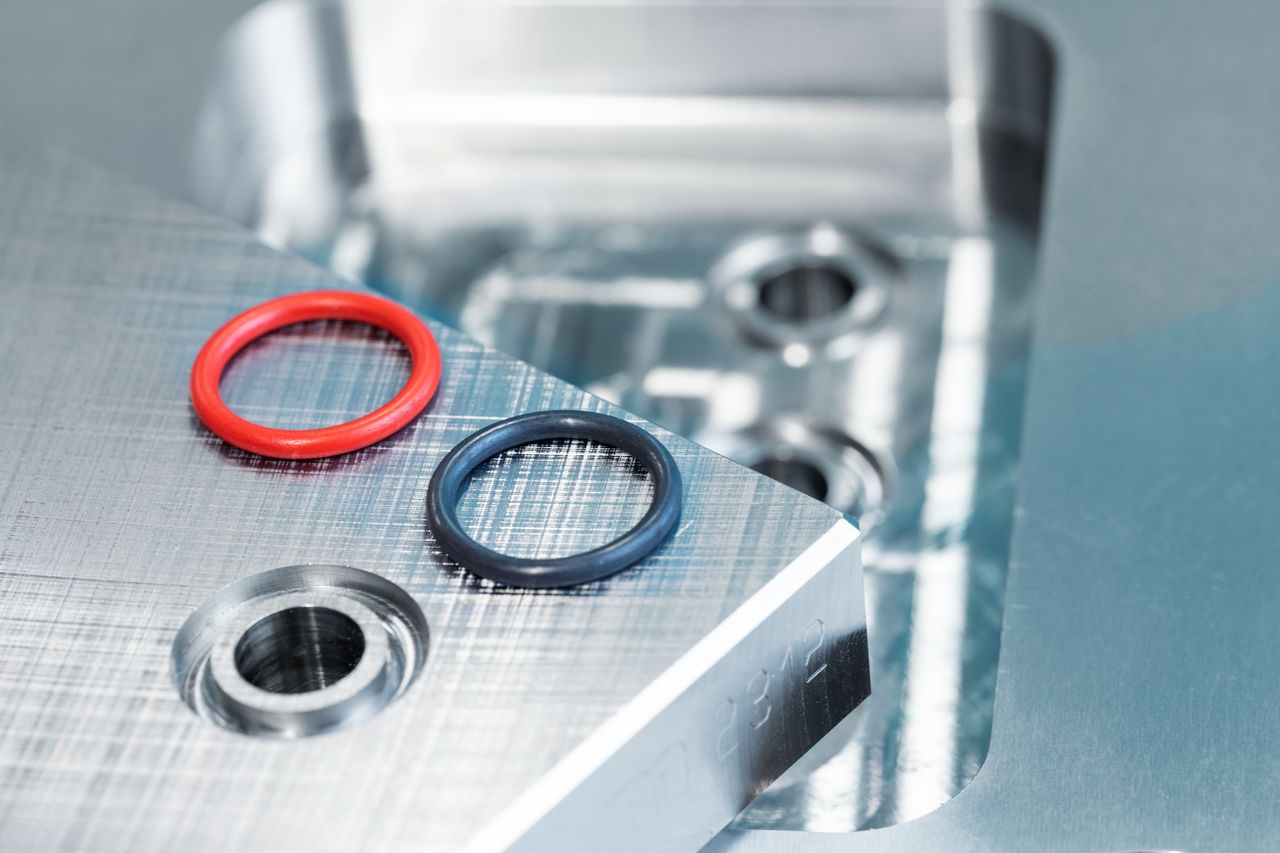
General information and selection
General information and selection
Use of O-ring seals
O-ring seals are mainly used in mould making to seal cooling holes used at plate transition or for components such as fountains and deflection elements. But O-ring seals can also be found in other components such as hydraulic cylinders and oil ports.
Dynamic and static sealing
A basic distinction is made between dynamic and static sealing. A dynamic seal is when the seal is created between components that move towards each other. O-ring seals are the optimum technical solution for dynamic sealing only in exceptional cases. For static sealing there is no movement between the components.
Axial and radial installation
The following figures compare axial and radial installation
Axial installation

Radial installation

In mould making, mainly static sealing is used with mostly axial installation. An example of this is the transition of the cooling holes from the cavity plate to the inserts.
Example of a mould insert

O-ring seal materials in mould making
The O-ring seals used in mould making are made of the material fluororubber - shortened to FKM, or FKM plus. FKM is generally very resistant to a variety of mediums and chemicals.
The selection of O-ring seal material depends mainly on the operating temperature. The usual FKM materials are used at water temperatures up to 100°C. If these were operated at water temperatures above 100°C they would harden, lose their elasticity and thus the pretension for the sealing effect. That’s why the special high-temperature O-ring seals made of the material FKM plus were developed for water temperatures over 100°C.
Planning and designing
Axial installation - circular pocket or ring groove?
The circular pocket offers the easiest and most space-efficient way to introduce an O-ring seal. However, the disadvantage is that the O-ring seal is always in direct contact with the medium (e.g. water or oil). This reduces the service life and shortens the maintenance cycles.

O-ring seal in a circular pocket: space-saving

O-ring seal in a circular pocket: more security
Advantage:
- Space-saving
Disadvantages:
- Contact with medium
- Abrasion
- Dirt build-up
The ring groove, on the other hand, completely separates the O-ring seal from the medium and thus offers maximum service life and long maintenance cycles. For optimal introduction, we recommend using an O-ring countersink, but it may also be carried out using a milling cutter.

O-ring seal in ring groove
Advantages:
- O-ring seal protected
- Long service life
- Concentric grooves when using countersink for O-ring
Disadvantage:
- Requires more installation
Specifications for the groove dimensions
The groove depth T1 is designed so that the cord size of the O-ring is pretensioned by 15-30%. The groove width B must guarantee that the cross section of the O-ring fills the groove to a maximum of 85% in order to provide reserves for swelling or thermal expansion. When pressure is applied from the inside, the O-ring seal should be in contact with the outside diameter, whereas when vacuum or pressure is applied from the outside, it should be in contact with the inner diameter.

Groove dimension for circular pocket

Groove dimension for ring groove
Tip: O-ring seal with a tight fit in the plate
The outside diameter D2 can be 1% to 3% smaller than the outside diameter d2 of the O-ring seal, so that the seal is tightly fitted and will not fall out.

In our groove recommendations, you will find the finished groove dimensions and the matching O-ring seals coordinated to the O-ring countersinks clearly displayed. This covers ≈ 90% of cases, saves time when searching and provides safety during use.
For your own groove design, you will find the recommended dimensions t1 and b on the respective O-ring seal catalogue pages E 2130 or E 21311.
Radial installation
For radial installation, we recommend a lead-in chamfer with 20°. You will find the appropriate dimensions B and T2 on the O-ring seal catalogue page. When drilling crosswise to the installation hole, the edges must be rounded. The O-ring seal may be stretched up to 6% when installed. For installation, the O-ring seal can be stretched up to 20% for a short time.

Production of the O-ring groove
Comparison: Production of the O-ring groove with a milling cutter or countersink for O-rings
A direct comparison shows that considerable time is saved when the groove is introduced using a countersink for O-rings. Furthermore, the difference in quality is clearly seen in the following figure. When produced with a milling cutter, milling grooves are created which run at the bottom across the groove. This is not optimal for sealing. With our countersink for O-rings, on the other hand, concentric grooves are visible which make optimal sealing possible. This saves time and provides security.

O-ring groove made with a milling cutter
Milling grooves criss-crossing the groove bottom hinder optimal sealing.

O-ring groove made with a countersink for O-rings
Concentric grooves ensure optimal sealing.
Countersink for O-rings at Meusburger
The countersink for O-rings ensures good accessibility in pockets (e.g. inserts) right up to the edge.We offer two types of countersinks for O-rings:


WZB 12112 Carbide countersink for O-rings
- Best groove surface quality
- Suitable for materials up to 54 HRC thanks to high-quality TiAlN coating
- Dimensions coordinated to provide a perfect fit for the O-ring seal on the outer diameter
- Available in the 4 most common sizes
WZB 32112 HSS Countersink for O-rings
- Can also be used on column drilling machines with the WZB 32113 pilot for countersink
- Available in 10 sizes

With our cutting data calculator you get the right cutting parameters in no time.To save you the time-consuming selection and matching of O-ring dimensions, O-ring grooves and matching countersink, you will find the appropriate combinations in our groove recommendations.
Installation, removal and maintenance
Installation and removal
No sharp or pointed objects may be used during installation and removal. This would result in damage to the O-ring seal and the O-ring groove. In addition, make sure that the edges of the O-ring grooves are burr-free and rounded. We recommend the practical, 5-piece V 28100 assembly tool set for O-rings. This not only saves you time, it also helps you with the installation and removal of O-rings in difficult and narrow installation spaces. A detailed description of how to use the tools can be found in our manual on the product page in the web shop.


Maintenance
In general, the O-rings should be replaced every time the mould is revised. When cleaning the mould, no cleaners with acetone should be used. This would cause the O-ring seals to become porous, which eventually leads to leakage in the mould. Our VCM 20 universal cleaner is optimal for cleaning O-ring seal installation spaces. Before inserting, check again that the O-ring seal will not be not fitted over sharp edges. Sharp edges should be rounded where necessary. When inserting, the O-ring seal can be stretched up to 20% for a short time.
Storage
When storing O-ring seals, the following conditions must be observed:
The storage temperature should preferably be between +5°C and +25°C and at a maximum relative humidity of 70%. Direct sunlight or bright light should be avoided. UV-protected storage areas or closed boxes are ideal. According to ISO 2230, the shelf life of O-ring seals made of FKM is a maximum of 10 years.