The described injection moulding problems are based on data and experience from Meusburger and the Plastic Centre (SKZ) in Würzburg.
The analysis of injection moulding problems is also available as an app. In addition, you will find numerous tips for the processing of plastics. Here, users can see where there is still potential for optimisation regarding the hot runner.
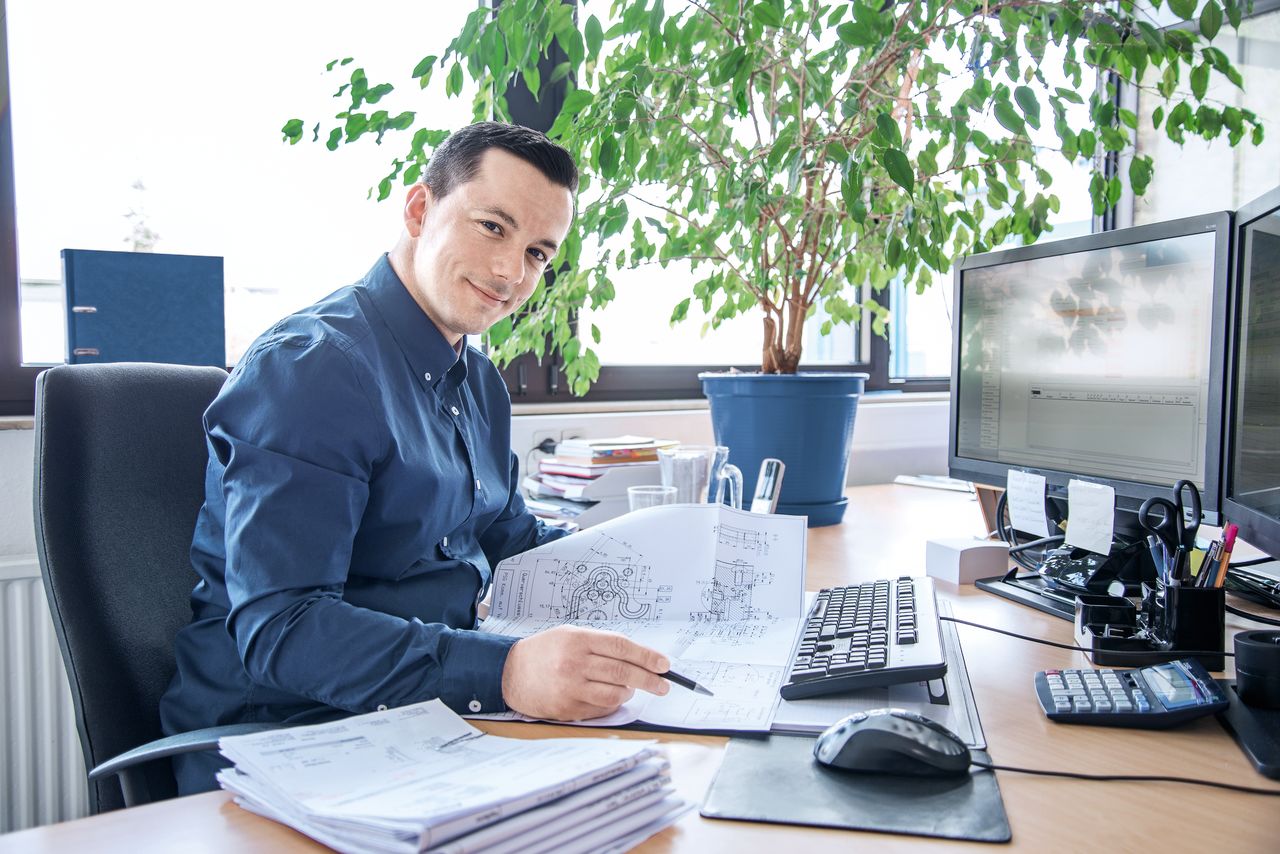
Burner effect /diesel effect
Burner effect /diesel effect
Visible by burn marks at the end of the flow path
Cause of defect:
If the air cannot escape out of the cavity during injection, it is compressed with high pressure by the melt. At the same time, the air is heated to such an extent (> 1000°C) that the air, the plastic and the steel can burn.
Burner/diesel effect error sources:
Material:
- Material releases particles, gases
- Additives, colours outgas
Method:
- Injection speed too high
- No injection profile, fast – slow
- Changeover point too late
- Locking pressure too high
- Dirty ventilation,
- Cleaning interval too long
Mould:
- Ventilation insufficient
Shrink marks
Shrink marks
Visible by slots (dents) in the surface
Cause of defect:
Shrink marks are caused by uneven mould shrinkage. They mostly appear at thick sections or at the end of the flow path.
Sources of defect:
Machine:
- Nozzle bore is too small
- Non-return valve worn
- Pressure control incorrect
Material:
- Plastic has too high shrinkage
Method:
- Holding pressure too low
- Holding pressure time too short (seal time)
- Mould temperature too high
- Injection speed too high
- Injection volume too low (change over point=too early)
- Residual melt cushion too small
Mould:
- Dimensions of gate and or gate insert wrong
- Too great differences in wall thickness
- Accumulation of melt (ribs too thick)
- Incorrect cooling configuration
Colour streaks
Colour streaks
There are two kinds of colour streaks:
1. Irregular colour streaks
The colour is insufficiently mixed: Visible by irregular coloured streaksEach part has a different hue.
Sources of defect:
Machine:
- Screw without shearing and mixing part.
- No mixing nozzle in use
- Cylinder too small
- Colour dosing appliance defective, not available
- Hopper is too large
- Colour charges itself electrostatically
Material:
- Master batch or pigments not compatible with plastic
- Solubility of the pigment insufficient
- Pigments, master batch granulate too large
- Plastic granulate too large
Method:
- Back pressure too low
- Melt temperature too low
- Colour dosing not sufficient
2. Colour streaks by separation
Here the coloured stripes are always in the same place.Colour pigments and plastic are not compatible or too high shear creates separation. Each part has colour streaks in the same place, majority in the area of flow lines.
Sources of defect:
Machine:
- Nozzle bore is too small
- Material
- Master batch or pigments not compatible with plastic
- Pigment thermally too sensitive
- Ratio of pigment too high
Method:
- Injection speed too high (too low)
- Melt temperature too low (too high)
- Mould temperature too low (too high)
- Back pressure, screw speed too high
- Colour dosing too high
Mould:
- Flow cross-section too small
- Flow path too long
- Position of flow lines unfavourable
- Gates too small
Colour difference
Colour difference
Irregular colour tone.
Cause of defect:
Visible by irregular colour tone. From one production to another, very often colour differences can occur.
Sources of defect:
Machine:
- Screw geometry
- Nozzle bore size incorrect, mixing nozzle missing/faulty
- Cylinder too small, too big
- Colour dosing appliance defective, non-existent
- L – D ratio different
- Injection control
Material:
- Batch to batch inconsistency of the material
- Colour pigments
- Drying for too long
Method:
- Back pressure too low.
- Melt temperature too low (or too high), inefficient temperature control
- Colour dosing not sufficient
Mould:
- Hot runner temperature profile is uneven
Jetting
Jetting
Visible strand formation of the injected melt on the moulded part surface.
Cause of defect:
If the melt does not come in contact with the mould wall, or it comes in contact too late, it does not fill the mould in a laminar flow. A melt strand is formed (worm track/snake) which is called “jetting”.
Sources of defect:
Machine:
- Nozzle bore is too small
Material
- Material too high viscosity
Method:
- Injection rate too high or
- no injection profile slow - fast
- Mould temperature too low
- Melt temperature too low
Mould:
- Unfavourable gate position
- Unfavourable gate dimensioning (too small)
- Changeover from gate - moulded part not rounded
Incomplete filled parts
Incomplete filled parts
Cause of defect:
Non-completely-injected parts at the end of flow length, at thin-walled section or at the venting of ribs This error often happens irregularly.
Sources of defect:
Machine:
- Nozzle does not seal against the mould.
- Non-return valve worn out
- Dosing inaccurate
- Specific injection pressure too low
- Draught on the machine
- Ambient air temperature fluctuates
- Heating power of the temperature control unit too low
- Regrind is not added homogeneously.
Material:
- Material too high viscosity
- Viscosity fluctuates
- Percentage of recycled material fluctuates
Method:
- Decompression too little, too slow.
- Injection pressure, holding pressure too low
- Residual melt cushion too small
- Injection volume too small
- Back pressure too low
- Screw speed too high
Mould:
- Wall thickness too thin, no flow aids.
- Gating system not balanced, too small
- Temperature control at hot runner inaccurate
- Venting within the tool not sufficient, blocked
- Hot runner nozzles (wearing of the tips/unequal nozzle lengths)
Defective surface gloss
Defective surface gloss
Cause of defect:
The more precisely the surface is reproduced by the plastic, the glossier the part in highly polished moulds and the more equally structured is the part when using etched moulds (no gloss/speck spots).
Sources of defect:
Machine:
- Specific injection pressure too low
- Temperature control unit issue, possible problem with tempering medium
- Material too high viscosity
- Injection speed too low
- Mould temperature too low
- Melt temperature too low
- Polishing of the mould surface insufficient
- Structuring of the mould surface insufficient
- Coating, material deposits, rust
- Differences in wall thickness
- Incorrect construction of cooling channels
Air bubbles
Air bubbles / air streaks
Bubbles inside the moulded part or streaks on the surface Cause of defect:
If there is air in the melt and it is injected into the cavity, air bubbles are formed inside the moulded part, which are visible in transparent parts. If these bubbles reach the mould wall during injection, they will burst open and become visible as streaks on the surface of the moulded part. Air bubbles and air streaks can occur at different places on the part.
Sources of defect:
Machine:
- Nozzle does not seal correctly
- No shut-off nozzle in use
Material:
- Material too high viscosity
- Inconsistent size of granulate
Method:
- Injection speed too high or too low or no injection profile slow – fast
- Mould temperature too low
- Melt temperature too low
Air hooks
Air hooks / tear drops
Visible by U-shaped flow lines after wall thickness changes or lettering
Cause of defect:
In the area of lettering, ribs, domes or sharp wall thickness changes, air which cannot escape quickly enough is swept along, overrun by the melt and embedded. Unexpected flow lines, so-called tear drops, occur.
Sources of defect:
Material:
- Material too high viscosity
Method:
- Injection speed in the critical area too high (too low)
- Mould temperature varies greatly
- Melt temperature too low
Mould:
- Mould venting not optimal
- No radii in critical areas
- Wall thickness changes too great
- Engraving depth too deep
- Cooling not sufficient
Matt spots in the gate area
Matt spots in the gate area
Often visible by matt surface in the gate/gate area
Cause of defect:
If the melt is injected very quickly and diverted by a sharp edge, large orientations and expansions of the molecular chains in the area of the gate area arise. The already solidified edge layer breaks open. This creates a matt area on the surface.
Sources of defect:
Machine:
- Speed regulation inaccurate
Material:
- Material too high viscosity
Method:
- Injection speed too high
- No injection profile slow - fast
- Melt temperature too low
- Mould temperature too low
Mould:
- Changeover from gate to cavity not rounded
- Gate diameter too small
- Gate position unfavourable
Disc grooves
Disc grooves
Visible by smooth grooves on the surface
Cause of defect:
If the melt is too thick (high viscosity) the plastic core expands in flow direction during injection. At the same time, grooves are generated in the surface layer. This effect can especially be seen at the end of the flow path.
Sources of defect:
Machine:
- Specific injection pressure too low
- Heating power of the temperature control unit too low
- Wrong selection of tempering coolant
- Draught on the machine
Material:
- Material too high viscosity
Method:
- Injection speed too low
- Injection pressure limitation too low
- Changeover point too early
- Mould temperature too low
- Melt temperature too low
Mould:
- Wall thickness too thin
- Flow paths too long, insufficient feed points
- No insulation plates
Flash
Flash
Visible by sharp edges or plastic film at mould splint lines
Cause of defect:
During the injection process, very high pressures are generated which can deform the mould and cause gaps to form at the split line face or in the areas of moving parts. If the melt gets into such a gap, flash or burrs can be produced.
Sources of defect:
Machine:
- Locking pressure too low
- Locking pressure uneven (bar wear)
- Locating ring hole too big
Material:
- Material too low-viscosity
Method:
- Injection speed too high
- No injection profile, fast – slow
- Volume of melt too large (change over point too late=pressure peak)
- Holding pressure too high
- Melt temperature is too high
- Locking pressure too low
Mould:
- Mould construction not rigid enough
- Mould split line surfaces damaged
- Split line face dirty
Visible flow lines
Visible flow lines
Clearly visible flow lines (notch)
Cause of defect:
If two melt fronts meet, they must fuse together. If they do not fuse together properly they leave visible notches. At flow lines colour separation often occurs (see coloured streaks).
Sources of defect:
Material:
- Material too high viscosity
- Colours – glitter particles too big
Method:
- Injection speed too low
- Holding pressure too low
- Melt temperature too low
- Mould temperature too low
- Changeover point too early
Mould:
- Bad venting
- Gate at wrong position
- No cascade gate system
Silvery streaks
Silvery streaks
U-shaped, drawn-out streaks / bubbles
Cause of defect:
If there is moisture in the granulate, water vapour is created during melting. These steam bubbles are visible in transparent parts. They are small, multiplied and present at different places of the part. Bubbles, which make it to the surface, can be recognised as u-shaped ‘smudged’ streaks, which are open against the flow direction. Plastic parts with moisture streaks are usually brittle.
Sources of defect:
Machine:
- Hopper is not covered
- No shut-off nozzle
- Dryer defect (in need of maintenance)
- Dryer too small
- Feed route for the material too long
Material:
- Residual moisture in the granulate too high
- Packaging defect of the granulate
- Additives are moisture-sensitive (soot)
Method:
- Decompression path too big
- Decompression speed too fast
- Pre-drying temperature too low /time too short
- Feed line too cold
- Mould temperature too cold
Mould:
- Mould leaking (cooling hole fissure)
- Flow cross-section too small
Stress cracks
Stress cracks
After some time, visible cracks appear in the part.
Cause of defect:
Stress is caused by different solidification times and pressures between the peripheral layer and plastic core. Stress cracks often occur after several days or weeks. See chapter: Shrinkage deformation.
Sources of defect:
Material:
- Material too brittle
Method:
- Mould temperature too low, too high
- Holding pressure to high, no profile
- Injection speed too high, too low
- Unfavourable changeover point
- Melt temperature too low, too high
- Inserts too cold
Mould:
- Unfavourable wall thickness ratio
- Flow path/wall thickness ratio too high
- Inappropriate position of the gate inserts
- Inappropriate cooling
Tiger Stripes
Tiger stripes
Tiger stripes on the visible surface
Cause of defect:
Light and dark stripes appear on flat parts, this effect can be seen especially at the end of the flow path. Tiger stripes particularly appear on PE and PP.
Sources of defect:
Machine:
- Nozzle bore is too small
Material:
- Wax ratio (paraffin) too high
- Wax (sliding and demoulding assistance) too thermally sensitive
- Integration of aggregates insufficient
Method:
- Injection speed too high (too low)
- Melt temperature too low (too high)
- Mould temperature too low (too high)
Mould:
- Flow cross-sections too small
- Flow path too long
- Position of flow lines unfavourable
- Gates too small
- Incorrect design of hot runner
Voids
Voids
Visible by bubbles, holes in the moulded part at the same place
Cause of defect:
Voids are generated by shrinkage inside the moulded part. They are at the end of the flow path or in thick areas. They are always at the same place in the moulded part. In transparent parts they are visible as bubbles.
Sources of defect:
Machine:
- Nozzle bore is too small
- Non-return valve worn-out.
- Pressure control imprecise
Material:
- Plastic has too high shrinkage
Method:
- Holding pressure too low
- Holding pressure time too short (solidification time)
- Mould temperature too high
- Injection speed too high
- Injection volume too low (change over point=too early)
- Residual melt cushion too small
Mould:
- Dimensions of gate and gate insert wrong
- Too great differences in wall thickness
- Accumulation of melt (ribs too thick)
- Incorrect cooling configuration
Burn marks
Burn marks
Cause of defect:
If the plastic is subject to too much thermal stress during pre-drying, plastification or injection, a degradation or change of the molecular chains can occur. This manifests in brown, black or silver streaks or marks. If the streaks are located at different places on the moulded part, they are probably caused during the drying or plastification stage. If they are always located at the same place, the cause is probably during the injection process.
Sources of defect:
Machine:
- Plastification unit too large
- Dead spots in the plastification unit
- Dead spots in the shut-off nozzle
- Nozzle does not seal correctly
- Nozzle bore is too small
- Percentage of recycled material too high
- Grit size too different (dust content)
- Plastic or additives, colour not sufficient or thermally stable
- Melt temperature is too high
- Back pressure, screw speed too high
- Residual melt cushion too big
- Injection speed too high
- Pre-drying too long, too hot
- Hot runner temperature too high
- Dead spots in the hot runner
- Hot runner system poorly designed
- Sharp edged transitions
- Flow cross-section too small