Für ein rationelles Wechseln von Werkzeugen in Fräsmaschinen wurden die dafür benötigten Aufnahmesysteme genormt:
- Steilkegel (SK)
- Hohlschaftkegel (HSK)
- Polygonschaftkegel (PSC)
Steilkegel
Vorteile
- Gut einführ- und lösbarer Steilkegelschaft
- Weitverbreitetes System
- Günstig
- Hohe Verdrehsteifigkeit
- Auch für Schwerzerspanung geeignet
(ISO 7388-1 und 7388-2)
Nachteile
- Geringe Steifigkeit
- Unsichere axiale Lage der Schneiden
- Begrenzte Genauigkeit
- Nicht geeignet für hohe Drehzahlen aufgrund technisch begrenzter Unwucht
- Regelmäßiger Austausch des Anzugbolzens aufgrund von Verschleiß
Hohlschaftkegel
Vorteile
- Hohe Steifigkeit aufgrund der Abstützung über den Bund der Werkzeugaufnahme
- Plananlage verhindert ein Verrutschen in Axialrichtung und sorgt für hohe Wechselgenauigkeit und sichere axiale Lage der Schneiden
- Kleine und leichte Bauweise erlaubt einfachen und schnellen Werkzeugwechsel
- Für hohe Drehzahlen geeignet
- Kein Anzugsbolzen notwendig
- Hohe übertragbare Drehmomente aufgrund
- kraftschlüssiger Drehmomentübertragung durch Kegel- und Anlagefläche
- formschlüssiger Drehmomentübertragung durch Mitnehmernuten/Bundnuten bei HSK A, HSK B, HSK C und Form D
Nachteil
Hohe Kosten
Steilkegel (SK)
Im Bereich Zerspanung ist der Steilkegel die weltweit meistverbreitete Schnittstelle zwischen Werkzeug und Werkzeugmaschine. Er zeichnet sich durch seine Kegelform aus, mit der die Aufnahme in die Maschinenspindel eingeführt wird.
Steilkegel nach DIN 2080
Steilkegel nach ISO 7388-1 (DIN 69871*)
Beim Steilkegel nach ISO 7388-1 handelt es sich um eine altbewährte Schnittstelle für Frässpindeln, die sich durch ihre Robustheit auszeichnet. Oftmals ist sie noch unter der bereits veralteten Normbezeichnung DIN 69871 bekannt. Die Spannung erfolgt bei diesem Steilkegel immer über einen zusätzlichen Anzugsbolzen. Der Werkzeugwechsel kann automatisch oder manuell stattfinden, während die Zentrierung ohne Plananlage über die Kegelfläche erfolgt.
Kühlmittelzufuhr nach ISO 7388-1:
- Form A: ohne Durchgangsbohrung
- Form AD: mit Durchgangsbohrung, für zentrale Kühlmittelzufuhr
- Form AF (Form B*): mit seitlicher Kühlmittelzufuhr über den Werkzeugbund
- Form AD/AF (Form ADB*): mit Durchgangsbohrung und seitlicher Kühlmittelzufuhr über den Werkzeugbund
Steilkegel nach ISO 7388-2 (JIS B 6339*)
Der Steilkegel nach ISO 7388-2 zeichnet sich ähnlich wie jener nach Norm ISO 7388-1 durch seine Robustheit aus. Des Weiteren erfolgt auch hier die Spannung mittels zusätzlichem Anzugsbolzen und die Zentrierung über die Kegelfläche ohne Plananlage. Der Werkzeugwechsel kann ebenso automatisch oder manuell stattfinden.
Grundsätzlich unterscheidet sich der Steilkegel ISO 7388-2 (JIS B 6339*) von jenem nach ISO 7388-1 (DIN 69871*) durch folgende Merkmale:
- Kegellänge
- Ausführung der Bundbreite
- Greiferrille
- Nuten für Mitnehmersteine
Kühlmittelzufuhr nach ISO 7388-2:
Form J: ohne Durchgangsbohrung
Form JD: mit Durchgangsbohrung, für zentrale Kühlmittelzufuhr
Form JF: mit seitlicher Kühlmittelzufuhr über den Werkzeugbund
Form JD/JF: mit Durchgangsbohrung und seitlicher Kühlmittelzufuhr über den Werkzeugbund
Kühlmittelzufuhr nach JIS B 6339*:
Form A: ohne Durchgangsbohrung
Form AD: mit Durchgangsbohrung, für zentrale Kühlmittelzufuhr
Form AF (Form B*): mit seitlicher Kühlmittelzufuhr über den Werkzeugbund
Form AD/AF (Form ADB*): mit Durchgangsbohrung und seitlicher Kühlmittelzufuhr über den Werkzeugbund
Steilkegel nach ISO 7388-2 (JIS B 6339*) mit Doppelkontakt
Der auf dem Steilkegel nach ISO 7388-2 basierende Kegel mit Doppelkontakt zeichnet sich dadurch aus, dass in gespanntem Zustand zwischen Steilkegel und Flansch der Spindel ein Kontakt hergestellt ist. Das sorgt für höhere Stabilität sowie Biegesteifigkeit. Bei der Verwendung dieses Kegels ist es jedoch notwendig, dass die Maschinenspindel für die Doppelkontaktverbindung ausgelegt ist. Informationen hierzu können direkt beim Maschinenhersteller angefragt werden.
* alte Bezeichnung
Hohlschaftkegel (HSK)
Hohlschaftkegel nach ISO 12164 (DIN 69893)
Eine Weiterentwicklung des Steilkegels ist der Hohlschaftkegel, bei welchem der Werkzeugwechsel ebenso automatisch oder manuell erfolgen kann. Was den Hohlschaftkegel besonders auszeichnet, sind die hohe Wechselgenauigkeit aufgrund der Plananlage am Bund und der engen Kegeltoleranzen sowie die kleine, leichte und stabile Bauweise. Durch die formschlüssige Kraftübertragung mittels Mitnehmernuten können große Drehmomente und ruckartige Belastungen aufgenommen werden. Er benötigt keinen Anzugsbolzen zum Spannen und ist für hohe Drehzahlen geeignet.
Diese HSK-Aufnahme ist in folgende Typen und Größen untergliedert:
Form A (DIN 69893-1)
- Für Bearbeitungszentren, Fräsmaschinen sowie Sondermaschinen mit automatischem Werkzeugwechsel
- Mit Greiferrille für automatischen Werkzeugwechsel
- Drehmomentübertragung über zwei Mitnehmernuten am Kegelende
- Zentrale axiale Kühlmittelzufuhr über Kühlmittelrohr
Geläufige genormte Kegelgrößen:
- HSK A-63
- HSK A-100
Form B (DIN 69893-2)
- Für Bearbeitungszentren, Fräsmaschinen für die Schwerzerspanung sowie Drehmaschinen
- Mit Greiferrille für automatischen Werkzeugwechsel
- Drehmomentübertragung über zwei Bundnuten, keine Mitnehmernuten am Kegelende
- Dezentrale Kühlmittelzufuhr über den Bund oder zentrale axiale Kühlmittelzufuhr über Kühlmittelrohr
Form C (DIN 69893-1)
- Anwendung vorzugsweise bei Spindeln in Transferstraßen und Sondermaschinen ohne automatischen Werkzeugwechsel oder Kurzbohrspindeln und Werkzeugverlängerungen sowie Reduzierungen
- Ohne Greiferrille für manuellen Werkzeugwechsel
- Drehmomentübertragung über zwei Mitnehmernuten am Kegelende
- Zentrale axiale Kühlmittelzufuhr über Kühlmittelrohr
Form D (DIN 69893-2)
Form E (DIN 69893-5)
- Anwendung für Hochfrequenzspindel (z. B. beim Graphitfräsen) und Holzbearbeitungsmaschinen
- Rotationssymmetrische Bauweise ohne Mitnehmernute
- Mit Greiferrille für automatischen Werkzeugwechsel
- Drehmomentübertragung rein über den Reibschluss
- Zentrale axiale Kühlmittelzufuhr über Kühlmittelrohr
Geläufige genormte Kegelgröße:
HSK E-40
Form F (DIN 69893-6)
Polygonschaftkegel (PSC)
Polygonschaftkegel nach Iso 26623
Beim PSC (Polygon Shank Cone) liegt das Hauptaugenmerk auf der Polygonform des Kegels. Diese sorgt bei der Drehmomentübertragung für einen gleichmäßigen Flächenkontakt zwischen Spindel und Werkzeughalter, was zu mehr Stabilität führt. Des Weiteren werden durch die dickeren Wandstärken im Vergleich zum HSK-Kegel größere Spannkräfte ermöglicht. Das sorgt für höchste Biegesteifigkeit, Drehmomentübertragung und Genauigkeit der Mittenposition. Polygonschaftkegel finden besonders bei Multi-Task-Maschinen (Drehen und Fräsen/Bohren) Anwendung, da die Position des Werkzeugs in der Aufnahme aufgrund des Polygons exakt definiert ist.
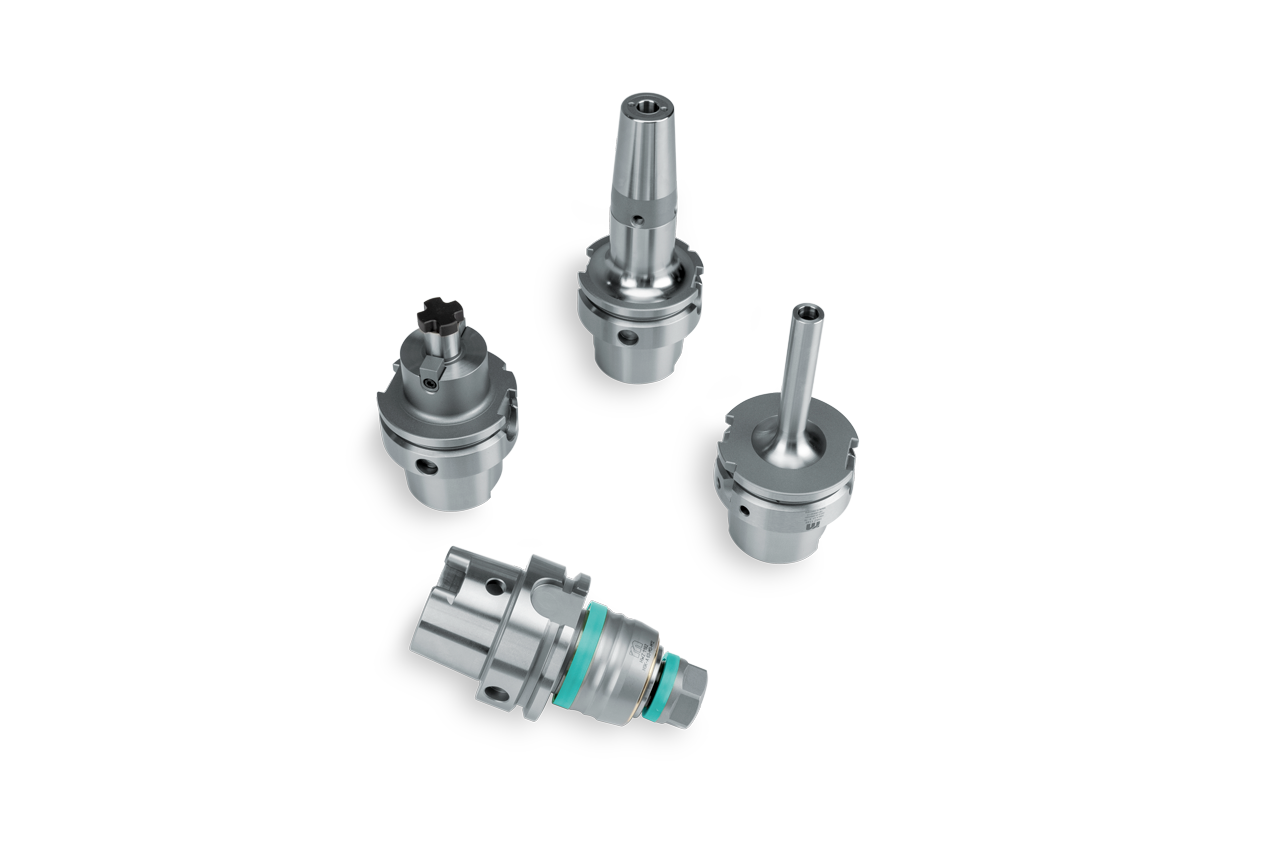
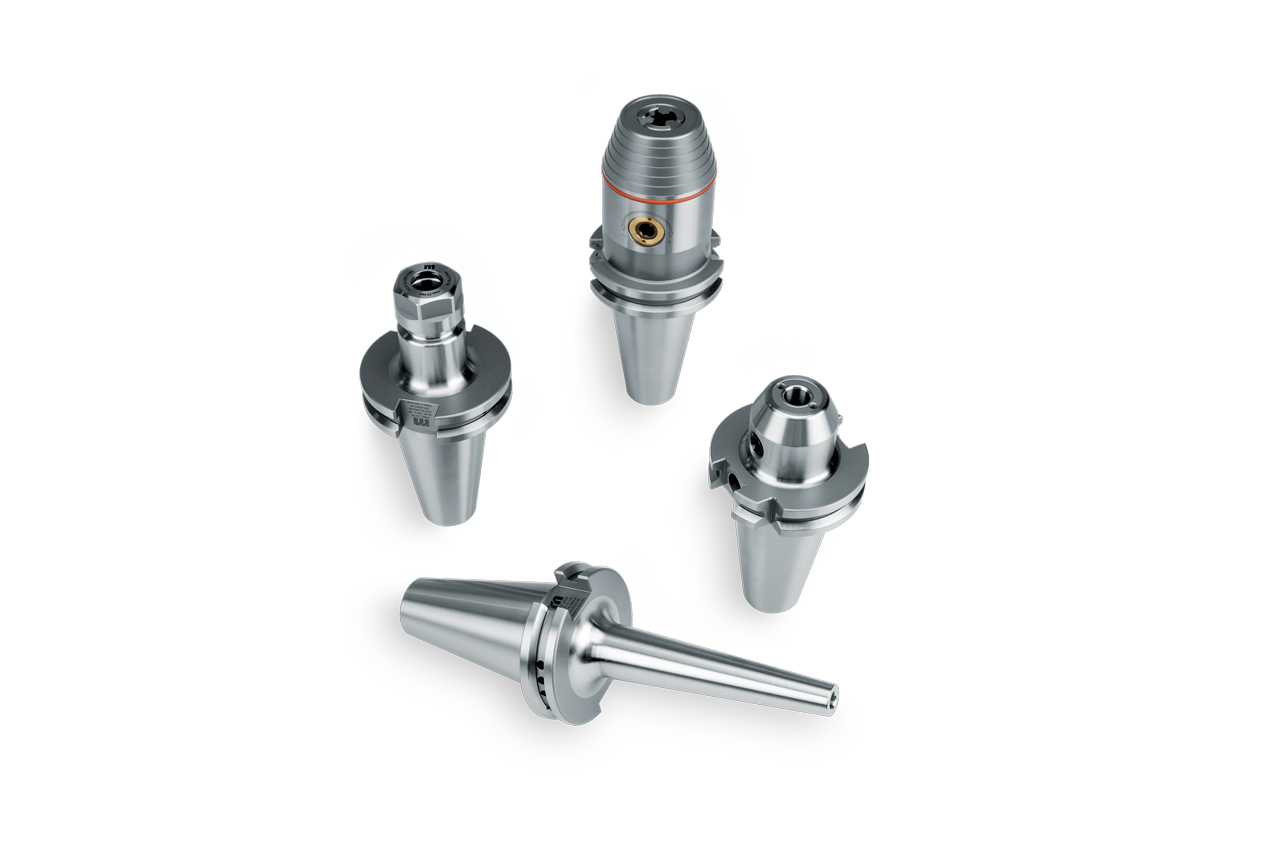
Sollte Ihre gewünschte Schnittstelle nicht verfügbar sein, können Sie deren Verfügbarkeit über Ihren Ansprechpartner anfragen.